
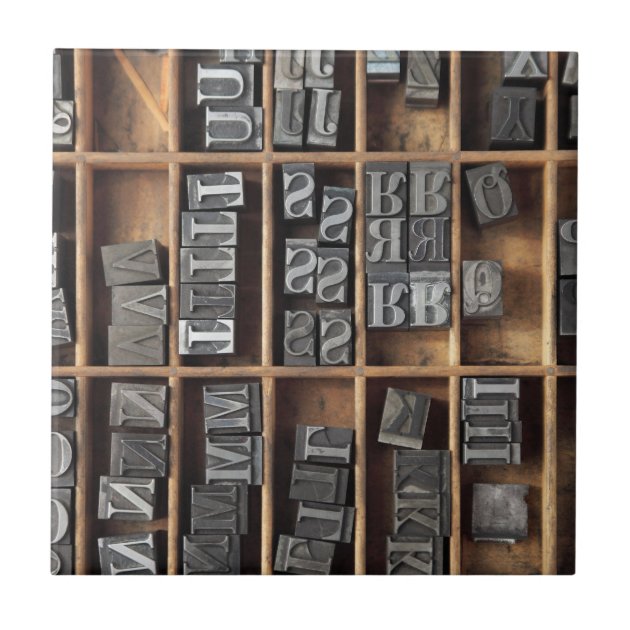
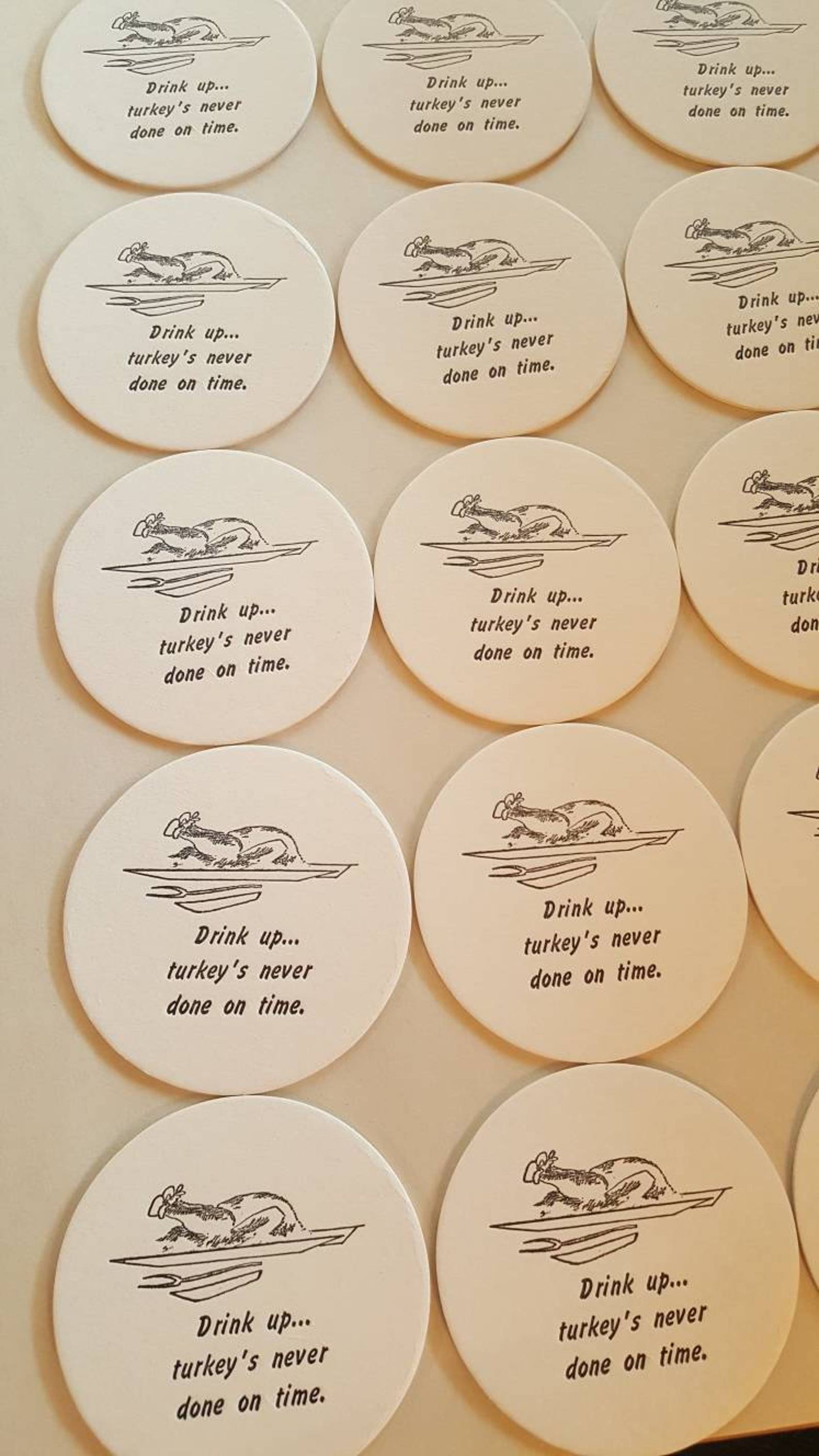
While copy was being typed the matrices (type moulds) were assembled within the machine. Linotype and Intertype took a similar approach: the operator sat at a keyboard and typed the copy. There were two broad approaches: build a complete line of type from a machine or build individual characters in the correct order from the machine.
#Letterpress typemetal driver
Composition TypeĪllowing printers to cast their own type was a key driver behind developments in composition type. That foundry alone had acquired Charles Reed and Sons in 1905, and H. The last of the English Foundries, Stephenson, Blake of Sheffield stopped trading in December 2004. The large number of small foundries gave way to a smaller number of large foundries. While early metal type from the continent (in particular Dutch type) was considered superior, the UK caught up and great names like Caslon, Figgins and Stephenson, Blake were established. The UK had a number of very influential foundries. There became two families of type: foundry type (generally harder quality) that was produced in the great foundries and composition type (slightly softer quality) that was produced from copy either by a specialist firm, or even by the printer himself. That’s to say go directly from the copy to the metal type with no sorting or composing process in between. As the 19th century grew to a close people we very keen to automate this part of the process-work began to look at producing type in the order it was needed. This composition activity took a great deal of time and tied up capital in the type needed. The key constraint for printers was that type from a foundry had to be assembled by hand before printing could begin.

The industry was centred around the demand in Fleet Street, London but other significant type founders worked where technical expertise was greatest-for example Stephenson, Blake of Sheffield. Type founding is a specialist industry needing artistic and design skills in equal measure with engineering prowess and ability to work in some of the very heavy aspects of industry. Type Founding in the Printing Economy in the UK Casting: this is filling the mould with molten type metal and removing the cast type.Creating the Matrix: this step takes the punch, and strikes it in a softer metal to make a negative mould.Modern-day equivalents of punches can be seen in DIY stores to mark metal equipment with initials. This skilled work requires a number of other punches and tools to be used to create the punch, and then it be subject to hardening. Punchcutting: creating a three-dimensional representation of the letter in the end of a bar of metal.There are three key stages in founding type – Gutenberg’s invention was the first to be exploited and the idea spread rapidly. Gutenberg of Germany is credited with the invention of moveable type around 1450 but records show that both Chinese and Korean inventors had used the idea before the time. When you practice letterpress printing it’s easy to forget just how difficult it must be for type founders to create tiny pieces of cast metal hard enough to withstand a tremendous force that are made to tolerances of less than one thousandth of an inch. Movable type was the breakthrough that allowed printers to use and re-use individual characters. Letterpress printing depends on a raised image, it’s known as a relief process.
